44Bogger
Member
Don't take offense to anything I say that might be common sense as I don't know everyone's skill level.
I did all that in less than 1.5 days without any assistance. The hardest part was getting the b pillar in and out without scratching the body. I could have gone to my dad’s and used his Lincoln but I tried out the Harbor Freight inverter that was given to me. Used 3/32” 6013’s. The combo worked better than the operator.
First thing I did was get a 2' piece of "scrap" 1.5" OD muffler pipe from the muffler shop.
Take out the seats. Don't do what I did and cut the b pillar too low trying to eliminate the lower piece welded to it. Just grind it off. Then cut a 5" section out of b pillar on each side with a chop saw. Cut above and below the upper welded on pieces. That keeps you from having to grind it off. Bevel the ends of the pillar where it will go back together.
Now cut 2 approximately 1' pieces of muffler pipe. Mark the approximate center with a sharpie. Tap a piece of muffler pip in each bottom piece of pillar. Tack the inner sleeves in so they don't move down while sliding the top/over piece on. Once the assembly is loosely back together set in back in jeep. I put 2 bolts back in each side. Then I used a pry bar to open an approximately 3/16" gap where the pillar joins together so the weld will tie the sleeve in. Use a fire blanket and tack the joints. Remove the assembly from jeep and weld it up.
Cut the rear mounting plate off the c pillar. Then cut about 4.75" off where you cut the plate off. Now put the plate back on the fender well and install just the rear bolt. Set the c pillar where it goes. Mark where to cut it in front of b pillar then do so. Set the c pillar back on jeep and see if the rear sets flush. I am no professional fabricator so I just kept making small cuts until it all lined up correctly. Remember you can cut again with less work then re welding pipe back on. Once you are happy with the angles weld it up. You won’t be able to use the OEM bolts the go in front of the rear mount. However you can install shorter bolts from underneath. Standard 5/16” bolts will thread thru the metric nut welded under the fender and you can place a nut on top of flange. The proper thing to do would be use matching metric bolts. You can cut the factory ones, just have to buy nuts.
I think the true professional way to do it would be to cut the b/c pillar mount flanges off and saddle cut the weld that joint up but that is beyond my ability/time level now. Can still do that at a later date.
I just hit the cleaned up welds with spray undercoating and no one notices.
Yes I could have welded plate over the front end of the c pillar but was too lazy. Went to tractor supply and got 2 1" plastic threaded caps. Cut the corners off the hex ends. Hit the caps with under coating and let dry overnight. Then I wrapped the threads in super 88 till it barely fit in the pipe. Yes don't laugh. I have a patent pending on the rear seat so don’t any of y’all be getting any ideas.
I live in South Louisiana and am fortunate enough to have garage space so a top isn't a big deal to me. However there has been alot of talk about tops on the forum and I can understand why.......yankees. IMHO, this is the setup that aftermarket hard top manufacturers should make a hard top and doors for. Only setup better would obviously be OEM Thar hard top with windshield but those may never make it across the pond.
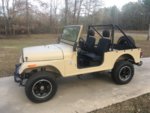
I did all that in less than 1.5 days without any assistance. The hardest part was getting the b pillar in and out without scratching the body. I could have gone to my dad’s and used his Lincoln but I tried out the Harbor Freight inverter that was given to me. Used 3/32” 6013’s. The combo worked better than the operator.
First thing I did was get a 2' piece of "scrap" 1.5" OD muffler pipe from the muffler shop.
Take out the seats. Don't do what I did and cut the b pillar too low trying to eliminate the lower piece welded to it. Just grind it off. Then cut a 5" section out of b pillar on each side with a chop saw. Cut above and below the upper welded on pieces. That keeps you from having to grind it off. Bevel the ends of the pillar where it will go back together.
Now cut 2 approximately 1' pieces of muffler pipe. Mark the approximate center with a sharpie. Tap a piece of muffler pip in each bottom piece of pillar. Tack the inner sleeves in so they don't move down while sliding the top/over piece on. Once the assembly is loosely back together set in back in jeep. I put 2 bolts back in each side. Then I used a pry bar to open an approximately 3/16" gap where the pillar joins together so the weld will tie the sleeve in. Use a fire blanket and tack the joints. Remove the assembly from jeep and weld it up.
Cut the rear mounting plate off the c pillar. Then cut about 4.75" off where you cut the plate off. Now put the plate back on the fender well and install just the rear bolt. Set the c pillar where it goes. Mark where to cut it in front of b pillar then do so. Set the c pillar back on jeep and see if the rear sets flush. I am no professional fabricator so I just kept making small cuts until it all lined up correctly. Remember you can cut again with less work then re welding pipe back on. Once you are happy with the angles weld it up. You won’t be able to use the OEM bolts the go in front of the rear mount. However you can install shorter bolts from underneath. Standard 5/16” bolts will thread thru the metric nut welded under the fender and you can place a nut on top of flange. The proper thing to do would be use matching metric bolts. You can cut the factory ones, just have to buy nuts.
I think the true professional way to do it would be to cut the b/c pillar mount flanges off and saddle cut the weld that joint up but that is beyond my ability/time level now. Can still do that at a later date.
I just hit the cleaned up welds with spray undercoating and no one notices.
Yes I could have welded plate over the front end of the c pillar but was too lazy. Went to tractor supply and got 2 1" plastic threaded caps. Cut the corners off the hex ends. Hit the caps with under coating and let dry overnight. Then I wrapped the threads in super 88 till it barely fit in the pipe. Yes don't laugh. I have a patent pending on the rear seat so don’t any of y’all be getting any ideas.
I live in South Louisiana and am fortunate enough to have garage space so a top isn't a big deal to me. However there has been alot of talk about tops on the forum and I can understand why.......yankees. IMHO, this is the setup that aftermarket hard top manufacturers should make a hard top and doors for. Only setup better would obviously be OEM Thar hard top with windshield but those may never make it across the pond.
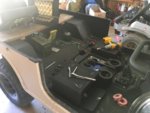
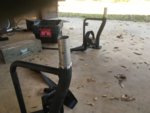
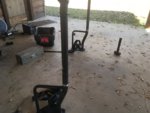
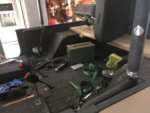
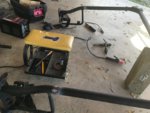
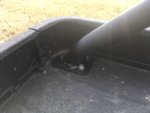
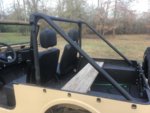
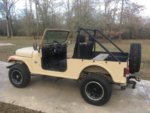
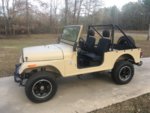